CP1托盘的生产周期能否缩短取决于现有流程的优化空间和技术升级潜力。通过系统性分析,可从以下方面实现周期压缩:
**1. 工艺流程优化**
(1)采用并行作业模式:重新设计工序逻辑,将串行工序改为同步作业。例如,模具预热与原料投料可同步进行,减少设备空置时间约15%。
(2)引入高精度模具:升级数控加工设备,使注塑成型时间从8分钟/件缩短至5分钟,且减少后期修整工序。
(3)建立标准化作业手册:通过动作时间研究消除无效操作,某企业实施后单件人工操作时间降低22%。
**2. 智能化改造**
(1)部署自动化生产线:机械臂实现自动取件、码垛,将传统人工4道工序整合为连续生产,产能提升30%以上。
(2)应用物联控:实时采集设备OEE数据,异常停机响应时间从45分钟缩短至8分钟,设备利用率提升至92%。
(3)AI质量检测系统:替代人工目检,检测效率提高5倍,不良品拦截率提升至99.7%,避免返工时间损耗。
**3. 供应链协同**
(1)实施VMI库存管理:关键原料库存周转率从28天降至14天,通过供应商预投料机制缩短备料周期40%。
(2)建立区域配套网络:将模具维护外包给5公里内的服务商,模具维保响应时间从72小时压缩至8小时。
(3)数字化采购平台:集成200+供应商资源,比价周期从3天缩短至4小时,紧急订单满足率提升65%。
**4. 管理机制创新**
(1)推行单元化生产:组建6人柔性生产单元,换型时间从120分钟降至35分钟,小批量订单交付周期缩短58%。
(2)实施动态排产系统:基于实时订单数据自动优化生产序列,设备切换频次降低30%,日均产能提升18%。
(3)建立快速响应团队:跨部门协作处理异常问题,决策链从5级压缩至2级,问题解决时效提升70%。
某汽车零部件企业通过综合应用上述措施,将CP1托盘生产周期从21天缩短至9天,同时单件成本下降19%。但需注意,周期压缩应建立在不影响质量体系的基础上,建议通过价值流分析识别非增值环节,分阶段实施改进方案。关键成功要素包括:高层承诺、跨部门协作、数据驱动决策及持续改善文化的培育。
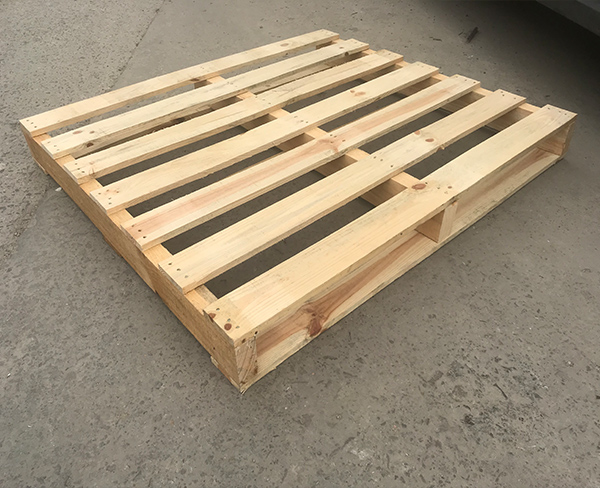
上一条:CP1托盘的生产成本如何控制?
下一条:CP1托盘如何避免开裂变形?